
Three Ways Automation Technology Can Improve Your Facility & Operations
Implementing automation in your systems and processes can have a big impact on your facility. Let’s take a closer look at three ways automation can improve your facility and operations.
Safety and Training | Power & Motion Technology | Crane Systems | by Peter Stipan | 16 Sep 2020
Do you have technology in place to help you plan maintenance to prevent costly downtime? Do your processes suffer from complexity that causes variations in product quality? Do you lack skilled operators who know how to prevent and correct load swing?
Implementing automation in your systems and processes can have a big impact on your facility. Let’s take a closer look at three ways automation can improve your facility and operations.
1) Increased Safety for Operators and Equipment
The safety of operators and equipment is paramount in any facility or worksite. Automation technology can help you build safety right into your equipment, systems, and processes to help prevent accidents from occurring in the first place. How? One way is through programmed safeties. Automated systems, like no-fly zone technology for example, allows you to designate areas where a crane should slow down or stop. This can help prevent suspended loads from injuring an operator or colliding with equipment. This also helps ensure consistent, predictable operation so workers know where loads are traveling and can work without needing to be aware of the crane’s path.
Automation technology can also help improve the working environment. If there are areas of the process that are dangerous, or have more potential to cause operator injury, automation technology can take over to prevent stop-work injuries and accidents. It can also prevent equipment failures from inconsistent or incorrect operation. Automation technology can also improve ergonomics for operators. Systems can be used to perform the more physically demanding work, so workers can focus on activities that demand greater skill. By reducing lifting, bending and other strenuous activity, operator fatigue can be reduced.
2) Maximized Uptime and Operational Performance
Time is money. Keeping equipment and processes running, and running efficiently, is critical. One way automation can help maximize uptime is by reducing cycle time. In a manual operation, the operator’s cycle time and the machine’s cycle time overlap. When a process is automated, the person is free to do other tasks or operate other machines while the automation is running, reducing overall cycle time. The automated machine can also do the same process over and over, without a break. This also helps reduce the operation’s cycle time.
Another way automation can maximize uptime is through predictive maintenance and reduced wear on equipment. Automation technology allows for communication between the machine and the operator or other key individuals in the facility. This allows for instantaneous data on how machines are being used and if there are any issues with equipment. With this information available 24/7, you can proactively schedule equipment maintenance. You can also understand if machinery is being used incorrectly and identify needs for operator training. For example, side-pull and off-center pick technology can be used to detect a load misalignment or snag condition and alert operators with a visible and audible warning before a dangerous situation occurs. By monitoring misalignments or snags, you have visibility into opportunities for process or operator improvement so they can be addressed.
DISCOVER OUR AUTOMATION SOLUTIONS
3) Improved Productivity and Product Quality
Companies are constantly in pursuit of low-cost, high-quality manufacturing. Productivity is important, and automation technology can help. Consistent and repeatable processes are key to increasing productivity. When processes are set up this way, you can increase production when demands peak. Automated production lines ensure speed, quality and consistency of operation, reducing, and even eliminating, error caused by process variation.
Automation technology can also reduce the risk of product damage, or waste. Automation produces the same result every time and decreases possible damage to a product from inconsistent processing. Automating critical processes helps manual operators work in cooperation with automated tasks, so products are handled less, thus reducing the risk of human error.
Combining our skills as lifting specialists with nearly 20 years of experience in automation technology from our Magnetek® brand, Columbus McKinnon is helping solve high-value problems that are important to your business.
Our automated crane systems are designed to improve safety, uptime and productivity in your facility. Not only does crane automation technology allow you to build safety right into equipment with no-fly zones and off-center pick prevention, it also provides you with real-time data and information that enables you to improve operational efficiency and make smarter decisions, faster.
Columbus McKinnon’s Unified and Magnetek brands bring more than 20 years of experience in delivering automated systems to the automotive industry. Our high-technology solutions are featured throughout the automotive manufacturing process, including ergonomic and autonomous workstations like ProPath™ and Intelli-Guide™.
Automated Systems
At Columbus McKinnon, we are dedicated to accelerating innovation and expanding our portfolio of automation and diagnostic solutions. One way we are doing this is through the development of intelligent automation solutions for new and existing cranes. See how our technology is helping to create the smart cranes of the future.
Lodestar VS with Intelli-Connect
The CM Lodestar VS is now available with Intelli-Connect™ Diagnostics and Analytics technology. Intelli-Connect enables quick and easy programming, maintenance, monitoring, and troubleshooting of the Lodestar – all from a tablet or smartphone.
How does it work? Using the Intelli-Connect Mobile and Mobile+ apps, you can wirelessly access detailed information right from the plant floor, without the need to attach a programming cable. Intelli-Connect is available as an option on all new Lodestar VS units or in a retrofit kit for units already in service.
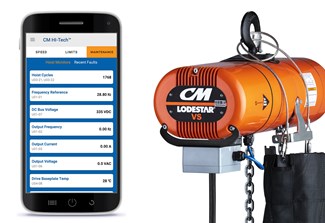
Related Articles
Understanding How Steel Mill Automation Can Improve Safety
By building safety right into the equipment, systems and processes running in the steel mill, you can keep operators safe and better informed of what is going on through every step of the process.
From cranes handling thousands of pounds of scrap steel to those transporting liquid metal at very high temperatures, the safety of both workers and equipment is critical in a steel manufacturing plant. By building safety right into the equipment, systems and processes running in the steel mill, you can keep operators safe and better informed of what is going on through every step of the process.
Safety in Automation
Columbus McKinnon Automation Experts, Jim Kluck and Peter Stipan, Discuss How Automation Improves Safety in your Facility
The second session in our Safe + Sound Week 2020 Virtual Speaker Series, Columbus McKinnon Automation Experts Jim Kluck and Peter Stipan discuss how automation can help improve safety throughout your facility.