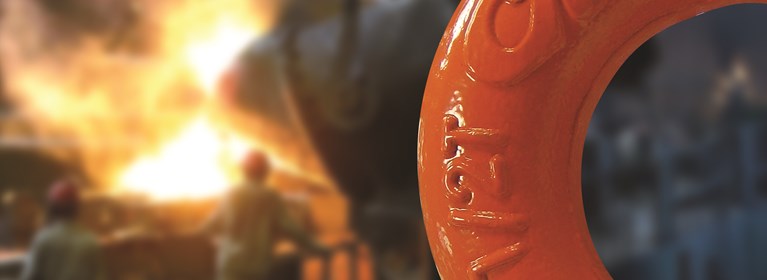
Nine Important Rules to Follow When Using Shackles
Learn the 9 essential rules for safe shackle use in lifting and rigging. Improve safety and comply with ASME/OSHA standards in your operations.
Rigging | Inspection & Maintenance | Safety and Training | By Columbus McKinnon | Jun 30, 2025
Shackles are critical components in nearly every rigging and lifting operation. Whether you're using them to connect slings, chain, wire rope, or lifting devices, it’s essential to follow best practices to ensure both safety and equipment longevity.
This guide outlines nine key safety rules for selecting, inspecting, and using shackles in industrial environments. Following these rules — along with manufacturer guidelines and OSHA/ASME standards — helps reduce risk and improve performance in your rigging operations.
Download the guide to have readily available at your worksite
Rule 1: Inspect Before Every Use
Before lifting, always inspect shackles for signs of:
- Missing or illegible identification
- Indications of heat damage, including weld spatter or arc strikes
- Excessive pitting or corrosion
- Bent, twisted, distorted, stretched, elongated, cracked, or broken load-bearing components
- Excessive nicks or gouges
- A 10% reduction of the original or catalog dimension at any point around the body or pin
- Incomplete pin engagement
- Excessive thread damage
- Evidence of unauthorized welding or modification
- Any other visible damage or condition that causes doubt as to the continued safe use of the shackle
Shackles showing any of these signs must be removed from service immediately. Regular visual inspections are essential to ensure continued safety.
For more details on when to remove a shackle from service, check out our Shackle Inspection Checklist
Rule 2: Never Exceed the Working Load Limit
Each shackle has a clearly marked Working Load Limit (WLL) — the maximum load it can safely handle. Exceeding this limit can cause failure and result in dropped loads, equipment damage, or injury.
Always base your rigging plan around the lowest-rated component in the lifting assembly.
NOTE: The angle of loading affects stress in the shackle. As the horizontal angle decreases, stress increases — and the effective WLL of the shackle is reduced.
Rule 3: Choose the Correct Type of Shackle
There are multiple shackle styles, each designed for specific uses:
- Anchor (Bow) Shackles – For multi-leg slings or side loads
- Chain (D-Shaped) Shackles – For straight-line loads only
- Screw Pin Shackles – Quick to install and remove
- Bolt-Type Shackles – For permanent, long-term, or vibration-prone applications
Choosing the correct shackle ensures safety and performance under your specific rigging conditions.
Rule 4: Align Loads Properly
Shackles are designed for straight-line tension across the centerline of the pin. Improper loading can reduce capacity or damage the hardware.
Avoid the following:
- Side loading, which reduces capacity significantly**
- Twisting or torsional force on the bow
- Uneven load distribution
Proper alignment maximizes strength and prevents premature wear or failure.
Note: Only anchor shackles may be side loaded. If a shackle is side loaded, the rated load must be reduced according to the manufacturer’s recommendation, applicable tables, or evaluation by a qualified person.
Rule 5: Use the Correct Pin and Secure It
Only use the original manufacturer-supplied pin. Never substitute pins from other shackles or components.
For proper use:
- With screw pin shackles, tighten the pin fully so the shoulder contacts the shackle body.
- With bolt-type shackles, ensure the nut and cotter pin are correctly installed.
Screw pin shackles must not be rigged in a way that causes the pin to unscrew. For vibration-prone applications, either:
- Tie-wire the screw pin
- Use a bolt-nut-cotter style shackle to prevent loosening
Rule 6: Avoid Shock Loading
Shackles are designed for the gradual application of load. Avoid any sudden force or jerking motion, which can exceed the shackle’s rated capacity and cause catastrophic failure.
Shock loading is especially critical to avoid in:
- Crane lifts over long spans
- Lifts involving moving or swinging loads
- Outdoor and marine environments
Rule 7: Follow Temperature and Chemically Active Environment Guidelines
Shackles must be rated for your operating conditions:
- Extreme cold may cause metal to become brittle
- High heat can reduce strength
- Chemically active environments (acidic or caustic fumes or substances) can degrade materials
Typical safe range for carbon steel shackles:
- -20°F to 400°F
For applications outside this range or involving chemicals, consult the manufacturer or a qualified person for derating guidelines.
Rule 8: Maintain Clear Markings
Do not use a shackle if any of the following markings are missing or illegible:
- Working Load Limit (WLL)
- Size
- Manufacturer identification
- Heat lot number (for traceability and quality control)
Columbus McKinnon shackles are manufactured with long-lasting markings and product traceability for safe and reliable use.
Rule 9: Remove Damaged or Questionable Shackles
Immediately remove from service any shackle that shows:
- Missing or illegible identification
- Indications of heat damage, including weld spatter or arc strikes
- Excessive pitting or corrosion
- Bent, twisted, distorted, stretched, elongated, cracked, or broken load-bearing components
- Excessive nicks or gouges
- A 10% reduction of the original or catalog dimension at any point around the body or pin
- Incomplete pin engagement
- Excessive thread damage
- Evidence of unauthorized welding or modification
- Any other visible damage or condition that causes doubt as to the continued safe use of the shackle
Important: Discard damaged shackles properly. Do not attempt to repair, bend, weld, or reforge shackles under any circumstances.
Shackles may appear simple, but they are subject to strict performance and safety standards. Failure to follow basic usage and inspection guidelines can lead to serious consequences, including equipment failure or injury.
Each of these nine rules helps ensure your shackles are used properly, inspected thoroughly, and operating safely within their intended load and environmental parameters.
At Columbus McKinnon, we provide industrial-grade shackles, rigging products, inspection services, and training programs to help keep your people, equipment, and operations safe.
Need help with inspection or training? Contact our rigging experts today.
Troy Raines
Troy Raines is Columbus McKinnon’s Chain and Rigging Product and Engineering Manager. He joined the company in 2005 as a general engineer, supporting quoting specials, product design, and manufacturing engineering initiatives.
Today, Troy plays a key role in the development and support of rigging products and contributes to several major industry standards. He is a member of the ASME B30.9 (Slings), B30.20 (Below-the-Hook Lifting Devices), and BTH-1 (Design of Below-the-Hook Lifters) committees. He also serves as an alternate on B30.10 (Hooks) and B30.26 (Rigging Hardware), and is active on multiple Web Sling and Tiedown Association technical committees, as well as ISO/TC 111/SC1 and SC3.
Outside of work, Troy is proud of his military service and his role as a father to three sons.
